Aim
- To test at what pressure a reinforced bottle will fail.
Experiment Setup
The standard hydrostatic burst test procedure was used to carry
out these tests. (See above)
The bottle re-enforcement
technique based on Richard Wayman's
technique described here:
http://wrockets.trib-design.com/index.php?project=RICHARD&page=hp
We used a
1.25L bottle with one half of
the jacket made from a
1.5L bottle, and the
second half (the neck) from another 1.25L
bottle. Because we don't have a heat gun we
used hot water instead to shrink the outer
bottle. It gave a very satisfactory result.
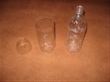 |
Re-enforcing a bottle with another bottle. |
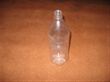 |
They loosely fit together, and then the
outer jacket is shrunk over the inner one. |
Results
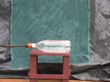 |
On the test stand. |
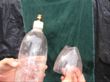 |
The top jacket separated. This will need a
bit more work. |
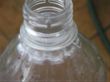 |
Stress fractures from 220 psi near the top
of the throat. The bottle did not break. |
We had three attempts at blowing it up
but on the first attempt the hose released
the nozzle at 160 psi. On the second attempt
a connector broke at a thread on our
pressure regulator at 200psi most of the
water was drained from the bottle through
the pressure bleed valve.
On the last attempt at 220psi the bottle
again separated from the hose, and although
there was virtually no air in the bottle,
the bottle took off and skidded along the
grass for about 15 meters. We will attach
the hose properly next time through a
different connector.
Conclusion / Analysis
Looking at the bottle after the tests it
was obvious that this is likely to be a very
good technique for building rockets that fly
at 200+ psi. The top part of the jacket
separated, but that is likely to be improved
with larger overlaps, and perhaps glue.
|