Date |
14th April 2007 11:30am -
2 pm |
Tested by |
GK and PK |
Location |
Sydney, Australia
|
Test Procedure |
Thrust
Measurement |
References |
N/A |
Related |
N/A |
Aim
- To measure the magnitude of the thrust produced by CD
(Convergent Divergent) nozzles.
- To compare the results to straight through nozzles.
Experiment SetupThe static test setup was identical to:
070406-001The thrust curve data shown below was for
a rocket with the following parameters:
Parameter |
Value |
Notes |
Capacity |
8.8L |
4 x 2L bottles joined
neck to base with a 8mm Robinson
coupling. The actual volume of each of
the 2L bottles is 2210mL |
Water |
2050ml |
For all tests.
The rocket used our Jet Foaming
technique to create foam. |
Bubble
bath solution |
50ml |
For all tests. |
Pressure |
100 psi |
For all tests (air) |
Because we were going to do quite a few
experiments, we didn't want all that foam
going into the garden so we collected the
water and in a large plastic tray under the
test rocket. We used up almost an entire
bottle of bubble bath for these tests.
Nozzle design
We manufactured two CD nozzles: one with
a 7mm throat and the other with a 9mm
throat. In both instances the expanding
section was 4 degrees from the centerline.
The expanding shape was conical since that
is much easier to manufacture. See diagram
at left. We didn't want to design an optimal
nozzle shape, we just wanted to see how much
of difference an expanding nozzle makes, if
at all, and only then would we attempt to optimise it.
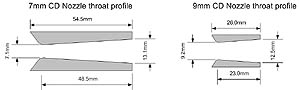
7mm and 9mm Nozzle
Profiles (click to enlarge)
The shape of the divergent section was
based on video footage of previous tests
where we measured the expansion rate of the
foam. We made the slope of the divergent
section less than the average slope in order
for the expanding foam to have some sort of an
"effect" on the nozzle.
We made sure that the baseline straight through
nozzles had exactly the same hole as the
minimum diameter (throat) in the CD nozzles.
This turned out to be 7.1mm and 9.2mm
respectively. This way we eliminated the bias due to
different sized holes.
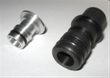 |
The 9mm and 7mm CD nozzles tested. |
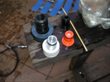 |
All the straight through and CD nozzles
tested on the day. |
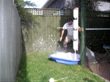 |
The foamy water is collected in a large tray |
Results
We ran three tests with the 7mm nozzle in
order to establish a baseline for the test.
The first test looks quite out of place
compared to the other two tests, and this we
traced back to forgetting to put in the
locking pin that prevents the dampner
container from moving. We believe the
fluctuations were due to this.
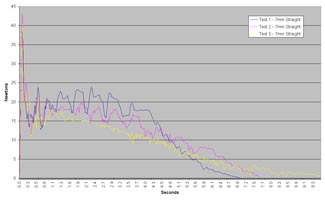
7mm straight through nozzle thrust curves
(click to enlarge)
When we performed the 7mm CD nozzle tests we
again repeated it 3 times in order to reduce
experimental errors and get a sense of
repeatability of the experiment.
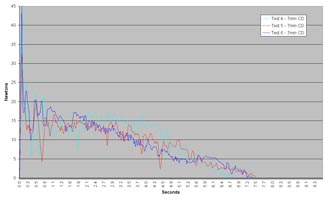
7mm CD nozzle thrust curves (click to
enlarge)
Now we average the two sets of data
(ignoring test 1) we get the following
graph:
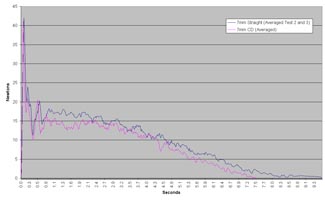
7mm straight through and CD nozzle thrust
curves
averaged and compared (click to enlarge)
We did not include test 1 in the average
because the measurements weren't reliable.
When we compare the straight through
nozzle performance to the CD nozzle
performance we see that with the 7mm CD nozzle
the total impulse is only
83% of
the straight through nozzle.
We then switched to the 9mm straight
through nozzle and ran another 3 tests. All
three tests showed similar results which
helped confirm that the test was
reproducible fairly accurately.
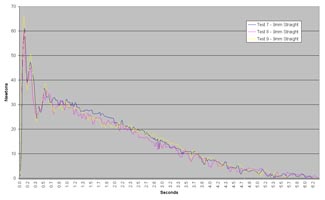
9mm straight through nozzle thrust curves
(click to enlarge)
Following that we performed another 3
tests with the 9mm CD nozzle. Again the
results were fairly similar to each other.
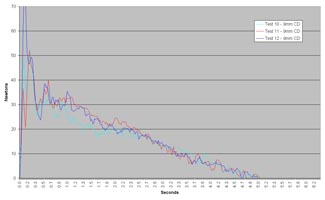
9mm CD nozzle thrust curves (click to
enlarge)
When we average the above
results for the straight through nozzles and
CD nozzles we get the following graph:
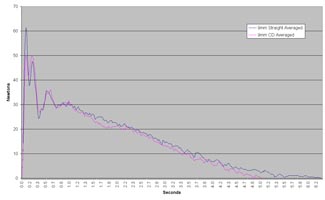
9mm straight through and CD nozzle thrust
curves
averaged and compared (click to enlarge)
The thrust curve shapes were almost
identical for the straight through nozzles
as well as the CD nozzles, however, it is
quite evident that the total impulse is
lower for the CD nozzles. In fact the 9mm CD nozzle
produced only 92.6% of the total impulse of a
straight through nozzle.
The results for both nozzles were
disappointing as we were hoping to see some
sort of improvement, however, the result was
not unexpected.
We must stress that these tests were done
at only 100psi and the results may be quite
different at much higher pressures.
Currently we do not have the technology to
make these tests at the high pressures we
think it is likely to make a difference
(1000psi+) Antigravity used their CD nozzles
with pressures over 1000psi.
The following graph shows the averaged
results for 7mm and 9mm nozzles. You can see
that the 9mm nozzles produced more total
impulse than the 7mm nozzles and would
therefore be better to reach higher
altitude.
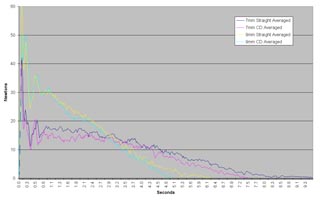
7mm and 9mm nozzles averaged and compared
(click to enlarge)
Should others want to do
further analysis of the data, the data for
both nozzles is available in spreadsheet
format here:
Thrust_Curves_140407.zip
Conclusions / Analysis
- It may be that because the foaming
agent affects the water's surface tension
it is causing the foam to "stick" to the
surface of the nozzle causing greater
friction. Different nozzle materials may
have a different effect on friction.
Perhaps the length of the expanding
section has an effect on the loss of
efficiency?
- It may be that the foam also isn't an
ideal foam and that a lot of loss of
impulse is due to normal water being
ejected. CD nozzles have a negative effect
when only water is used.
- It may also be possible that the
shape of the nozzle has to be quite
different compared to what was tested
here.
- One thing that is not evident from
these results is that the total thrust
does not end with the end of the thrust
curve. In fact, a decaying amount of
thrust usually continued for
another at least another whole second. But the thrust
was less than the weight of the rocket and
so is not shown on the graph. In real life the rocket would actually
decelerate less slowly during this time due to drag
and gravity then if
the thrust had ended completely.
- Some of the variance in the results is
also due to how the water was distributed
between the lower and upper bottles for
the Jet foaming to be effective. It is
difficult to accurately control the ratio
of the water in the two bottles.
- Because both the 7mm and 9mm CD
nozzles gave a lower performance than
the straight through nozzles, we will
put further testing and development of
CD nozzles on the back burner until we
can reach much higher pressures and then
test again.
Test Record
Test |
Pressure (psi) |
Total Impulse(N-s) |
Notes |
1 |
100 |
97.0 |
Calibrated test, 2050ml water, 50ml
bubble bath 7mm straight through nozzle. |
2 |
100 |
94.9 |
Calibrated test, 2050ml water, 50ml
bubble bath 7mm straight through nozzle. |
3 |
100 |
82.0 |
Calibrated test, 2050ml water, 50ml
bubble bath 7mm straight through nozzle. |
4 |
100 |
77.0 |
Calibrated test, 2050ml water, 50ml
bubble bath 7mm CD nozzle. |
5 |
100 |
70.7 |
Calibrated test, 2050ml water, 50ml
bubble bath 7mm CD nozzle. |
6 |
100 |
72.5 |
Calibrated test, 2050ml water, 50ml
bubble bath 7mm CD nozzle. |
7 |
100 |
97.3 |
Calibrated test, 2050ml water, 50ml
bubble bath 9mm straight through nozzle. |
8 |
100 |
91.2 |
Calibrated test, 2050ml water, 50ml
bubble bath 9mm straight through nozzle. |
9 |
100 |
95.5 |
Calibrated test, 2050ml water, 50ml
bubble bath 9mm straight through nozzle. |
10 |
100 |
82.8 |
Calibrated test, 2050ml water, 50ml
bubble bath 9mm CD nozzle. |
11 |
100 |
89.6 |
Calibrated test, 2050ml water, 50ml
bubble bath 9mm CD nozzle. |
12 |
100 |
90.7 |
Calibrated test, 2050ml water, 50ml
bubble bath 9mm CD nozzle. |
|