Aim
- To test at what pressure the hybrid splice will fail at.
Experiment Setup
The standard hydrostatic burst test procedure was used to carry
out these tests. (See above)
Hybrid Splice Background
See the following link for discussion on the Hybrid splice
concept:
http://www.aircommandrockets.com/day47.htm#hybrid_splice
The total cross-sectional area of all the
holes was equivalent to a 32mm Robinson coupling.
That is about 15 times bigger than our
typical 8mm coupling.
We spliced two 1.25L bottles and let it dry for about 4 days
and then performed a hydrostatic burst test on it.
Results
The splice held up to 130 psi. The sleeve was held
down by a combination of PL Premium and VISE
glues. After we put the PL glue in we
noticed there were a couple of minor leaks,
so we poured the runny VISE glue in to fill
those, and that sealed it well.
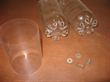 |
Hybrid splice components. |
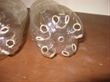 |
Detail of the location of the holes in the
base of each bottle. |
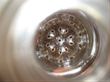 |
An inside view of the same holes. |
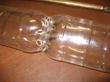 |
Bottle bases screwed together using a single
bolt through the middle. |
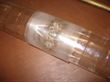 |
sleeve and bottles sanded ready for gluing. |
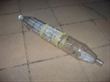 |
Glued and cured splice 4 days later ready
for test. |
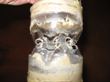 |
sleeve cut away showing where the splice
failure occurred. Note the cracks between the
holes. |
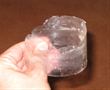 |
Half of the cut away sleeve. You can see
where it ripped all the way around. |
It is unclear what the initial failure
point was but both bottles cracked between
the holes in the bases and the sleeve also
ripped all the way around. It did not
delaminate from the glue, the plastic
failed. After a number of discussions with
forum members we now suspect the failure was
at the sleeve first and when that failed the
bottles did. Normally a sleeve like that
should hold at least 180-190psi. The bottles
still remained together and no shrapnel went
flying. It looks like the holes in the sides
have weakened the bases too much.
It was a really unusual failure because
the sleeve edges are still attached to the
bottles all the way around. The straight
edge seen on the torn sleeve photos is from
the scissors when I cut the sleeve away to
photograph the inside.
Conclusions / Analysis
If the sleeve failed first that means
that the bolt wasn't doing a good job of
holding the bottles together. When we first
bolted the bottles together we noticed that
there was a certain amount of give. The
bottom of the bottles flexed a little when you
pulled on the two ends. This was seen before
gluing the sleeve on. With the one bolt,
this flex in both bases was probably enough
to put most of the strain on the sleeve when
pressurised. Because the pressure was the
same on both sides of the lobes you didn't
get the typical crack propagating from the
central bolt hole but rather the
circumferential cracks between the weakest
points.
130psi is not all that great for this particular hybrid
design when you consider the VISE glue-only splice held
170psi+ and our Robinson couplings hold also
around 170psi+ with bottle burst pressures
around 190 psi. A 130psi splice means about
100psi operational pressure.
The reason the sleeve may have failed at
a lower pressure is that because the sleeve
is only really held down by the ends. The
middle could have bulged out under pressure,
and placed uneven strain on it. With a
normal splice the sleeve is completely held
down along its full length by glue and so
this bulging is unlikely to happen.
The cross-sectional area of the bottles
is 63.6 cm2 and at 130 psi you
end up with a force of 581Kg pulling one
bottle in one direction and the same in the
other direction. No wonder you get a bit of
flex in the base of the bottle.
As a result it may be better to try the
Robinson coupling Pat suggested in the first
place for the hybrid splice. Although the
coupling may experience the same flex at the
base of the bottle, putting the strain on
the sleeve again. It may achieve better
results since the bottles are not weakened
by the holes in the lobes. |