Aim
- To measure the internal temperature of a bottle
undergoing pressurisation in order to determine if the
heating due to pressurisation can cause a bottle to fail at
a lower pressure.
Theory
The strength of PET material used in bottles is
affected by temperature. The lowest
temperature where this effect begins is
known as the
glass transition temperature. Wikipedia
lists this as both
75 degrees C and
69 degrees C (see table) however, the
actual value depends on a number of factors
such as additives and the microstructure of
PET.
The main question is whether under normal
circumstances a rocket made out of PET
bottles can reach such a high temperature
where the rocket can fail at a lower
pressure compared to the same bottle tested
hydrostatically. Due to the nature of
hydrostatic testing the bottle is cooled by
the water and hence does not experience the
same sort of heating as a rocket on a launch
pad.
A number of factors can affect the
temperature inside the rocket and hence the
walls of the bottle.
Sources of heat include:
- Sun - With the greenhouse
effect the sun can raise the temperature
inside the bottle above the outside
ambient temperature. It is the same
effect as you get in a closed car on a
hot day. The colour of the bottle or any
dark paint or tape on it can have a
significant effect on the internal
temperature.
-
Pressurisation - By far
the largest contribution to the
increase in temperature inside the
rocket is due to pressurisation. As
air is compressed the temperature
increases.
-
Air source - The air
supply type also has a contributing
factor to the temperature. When
filling from a compressor, the air
is heated by the compressor, and
warm air comes out of the air hose.
When filling from a tank, the air
comes out cooler due to expansion. The higher the rate of
flow the cooler it is. The length of
hose also has an effect on heating
or cooling the air from the air
source. A long black hose can also
heat the air when exposed to the
sun.
-
Bottle stretching - As the
bottle is pressurised and the walls
stretch, that process in itself
may generate some heat in the walls.
(Thanks Christian and Trevor for
pointing that out)
-
Ambient temperature - This
is the outside air temperature. This
can be significant if you are
launching on a hot day.
Experiment Setup
The thermal tests were performed on a
spliced pair of 1.25L bottles. The air was
let in through the bottom and the thermocouple
was fed in through the top lid and suspended
about 15cm below the lid.
The thermocouple was connected to the
multimeter set on its thermometer
setting. We also placed a watch next to it
and a pressure gauge that read the line
pressure fairly close to the bottle inlet.
We set up a video camera to simultaneously
record the temperature, time and pressure
relationships.
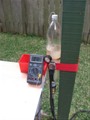 |
2.1L spliced-pair under test. With pressure gauge,
temperature gauge and a watch. |
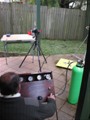 |
Air is supplied from a SCUBA tank through a
pressure regulator. |
Results
We filled the bottle at different
rates to around 100psi. In some tests, we also filled the
bottle with ~800ml of water which
would typically be found in a rocket this
size. The air bubbled through this column of
water as would happen on a launch pad.
Thermal tests
The ambient temperature was 12 degrees C on
the day of the tests.
Test |
Air
Supply |
Test |
Start
Temp
(deg C) |
Max
Temp
(deg C) |
Pressure
(psi) |
Time to reach
max pressure |
1 |
Tank |
Air only |
12 |
35 |
110 |
36 seconds |
2 |
Tank |
Air only |
12 |
33 |
105 |
28 seconds |
3 |
Tank |
Air only |
12 |
33 |
100 |
16 seconds |
4 |
Tank |
Air and Water |
12 |
33 |
95 |
14 seconds ** |
5 |
Tank |
Air and Water |
12 |
32 |
95 |
13 seconds ** |
6 |
Compressor |
Air only |
12 |
21 |
30 * |
52 seconds |
Test results
*We only managed to get to 30psi with the
little compressor before it decided to
splutter and seize up.
** Fills faster because of the reduced
volume.
Other Tests
- We measured the temperature
of the air coming out of the hose before
entering the bottle. During a slow fill rate
the air temperature was close to ambient. On
maximum flow rate the temperature reached 7
degrees C which was 5 degrees below ambient
temperature.
- Three months ago we ran some tests on
small compressors to measure the air
temperature coming out. The ambient
temperature at the time was 17 degrees
C. The temp started out okay when the
compressor was first turned on at around
18 C. After about 2 minutes of unloaded
operations (the compressor wasn't
filling a rocket) the air temperature
climbed to 29 C. At that point I stopped
the test. That was a 12 C increase
without any load.
- On one occasion after air had cooled in the
pressurised bottle, we let the pressure out
rapidly and the air temperature dropped to
-1 degree C.
Conclusions / Analysis
- From these few tests it is difficult to
reach definitive conclusions about whether
it is possible to reach 70 degrees in the
bottle.
Filling to higher pressures of 130 -
140psi will also have an effect on
further increasing the temperature.
On a hot day filling to higher
pressures would certainly be within
the ball park figure of exceeding
the glass transition temperature,
but we won't be certain until
further tests.
We
have observed an
unusual stretch failure last year when
we tried launching a rocket on a very hot
day where temperature was around 40C and
pressurised to 130psi.
- We were quite surprised that the
higher flow rate into the bottle did
not increase the air
temperature, but this could be
partially explained by the fact that
at the higher flow rates the air was
5 degrees cooler when it entered the
bottle. Faster filling from a
compressor could be different.
-
We were unable to test even
faster flow rates mostly due to our
air supply setup in that it has a
number of quick release connectors
with relatively small holes.
-
The other interesting result was
that filling the rocket through the
water column did virtually nothing
to cool the air being compressed
above the water.
-
Other consequences of filling
rapidly and heating the air,
especially on bottles sitting behind
non-return valves is that the air
pressure will drop once the air
cools inside the rocket. Depending
on various factors this could be as
much as 10psi. This is particularly
significant if you wait for a while
before launching a rocket.
-
Because filling a rocket rapidly can
raise temperature significantly it is
advised to fill a rocket slowly to allow the
air to cool.
|